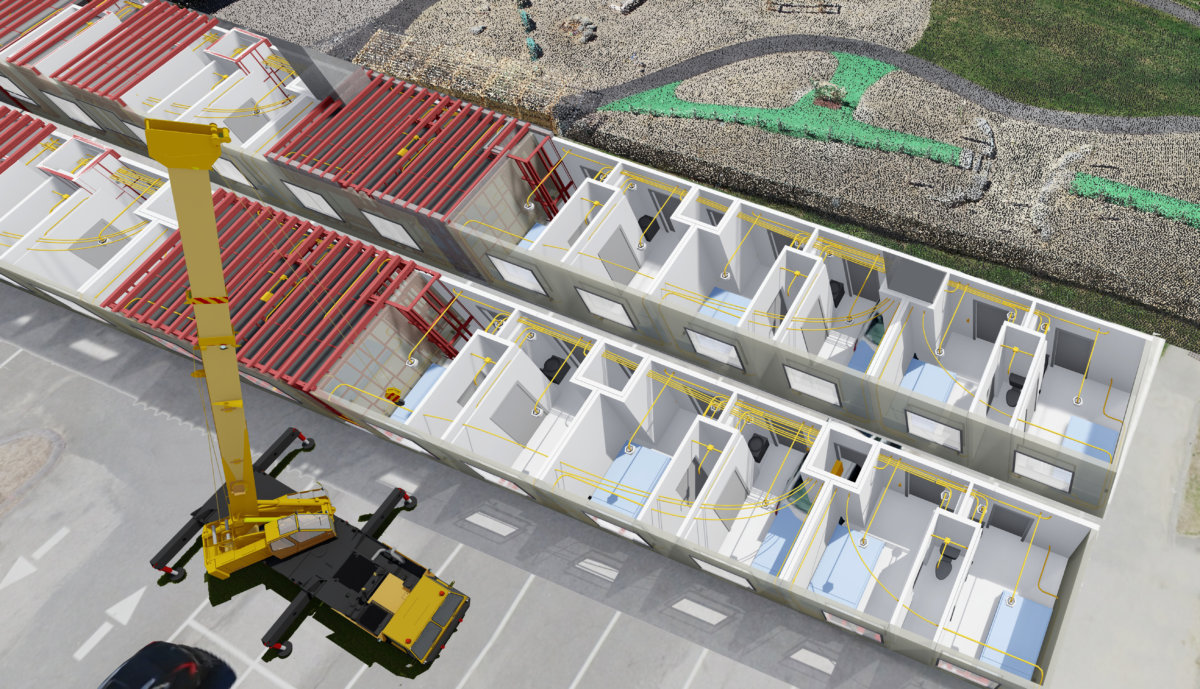
In a summer filled with uncertainty, especially for academic institutions, Windover Construction collaborated with several academic clients to help create a safe environment for students to return to this fall. Windover helped these schools and universities with planning, budgeting, permitting, and constructing isolation housing – all in a matter of months – by combining leading-edge technology with in-house volumetric modular construction expertise.
Given the immediate need to have these buildings in place for quarantined students during the fall semester, Windover combined leading-edge reality capture technology with BIM/MEP coordination and 4D animations to streamline decision making and expedite schedule, permitting, and implementation of the isolation housing on each campus.
With the use of drone mapping and laser scanning, Windover was able to capture detailed topography and existing conditions data of each campus. This data was processed quickly to give clients information-rich 3D models and overlays for coordination within just hours of laser scanning. Through this integrated 4D planning, clients and project teams were able to determine the best location on campus for the modular units.
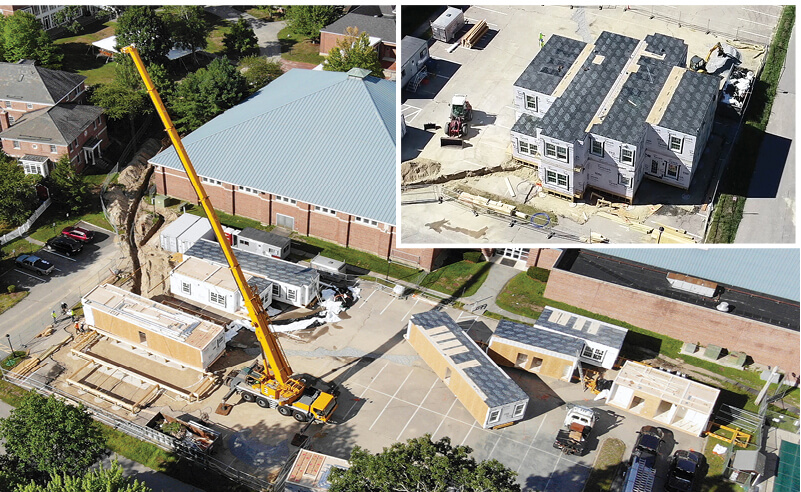
In addition, Windover utilized data from the scans in conjunction with 3D models to help clients determine the best layout for the modular units. From these models, 4D animations were created that streamlined the decision process by allowing project stakeholders to clearly visualize each technical and aesthetic aspect of the project. This was crucial in ensuring permitting was approved to maintain the tight schedule. For example, the fire permit process was expedited by using a 3D animation to show fire department officials exactly how a fire truck would access and exit the site in case of emergency.
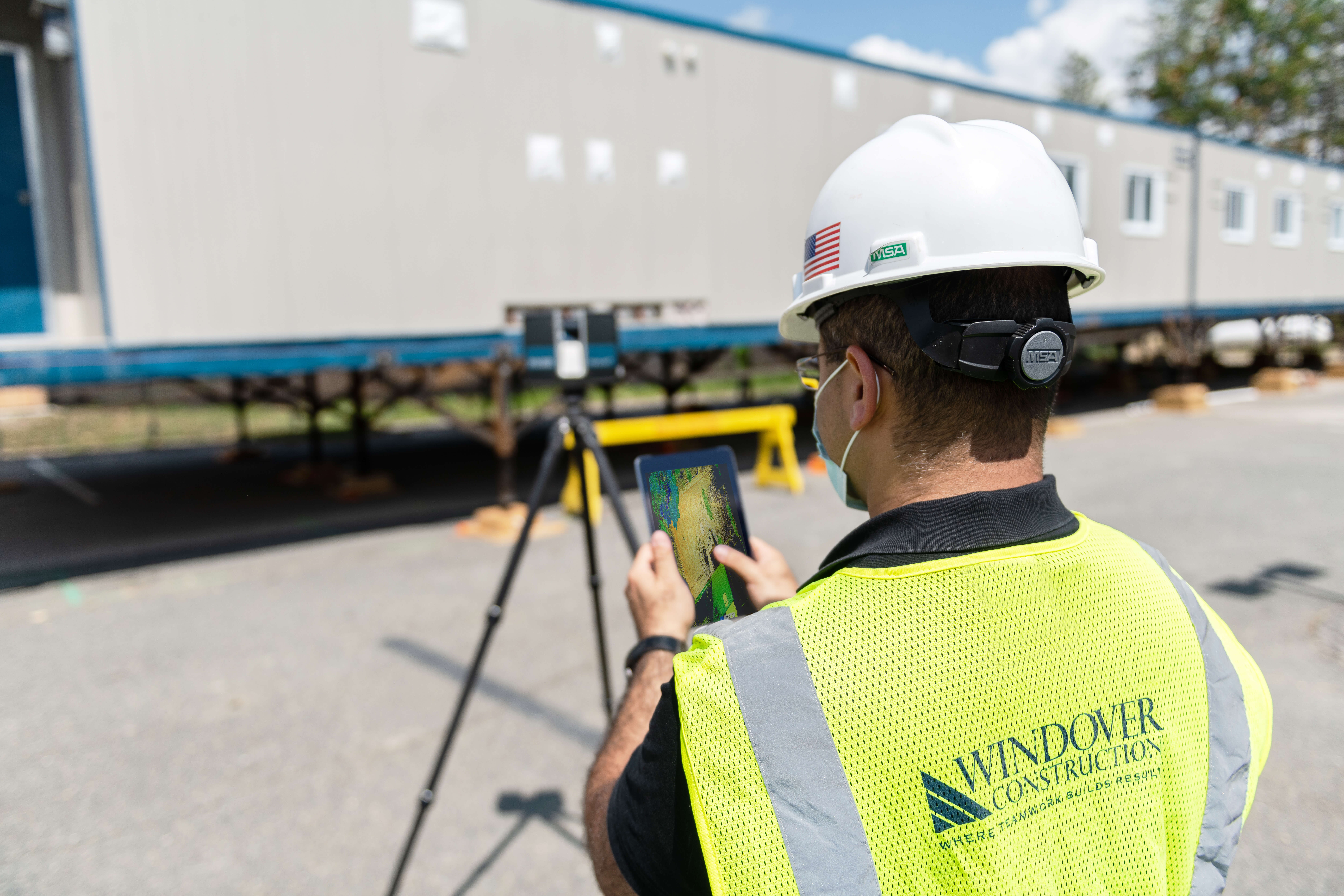
Windover utilized reality capture data combined with BIM to help prepare these sites for the onsite construction and installation of the modular boxes, especially planning underground utilities layouts. The data captured with these applications in the early phase of the project – and captured in a fraction of the time compared to traditional methods – mitigated risk and allowed for seamless onsite installation of the modular boxes. Finally, when the modular units arrived, they were scanned to create 3D as-built scans to provide documentation for future re-purpose and maintenance.
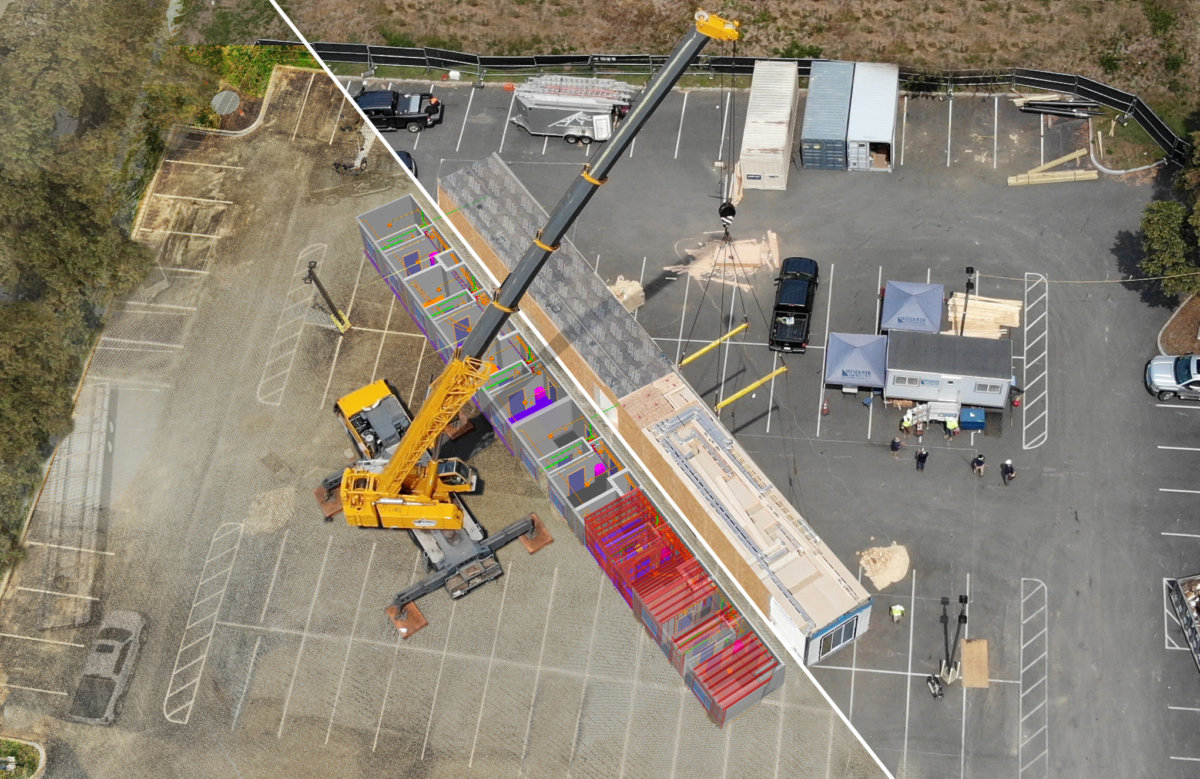
With thorough coordination and planning, made possible by utilizing this leading-edge technology, Windover was able to help academic clients respond quickly to the need for isolation housing – from concept to construction – in only a few months.
To learn more about how Windover is “Building on Data” and why capturing and integrating data was critical in these fast-tracked projects, check out this article from Inside Unmanned Systems.
Find this story in a construction news roundup from our partner, Buildr!